Производственный процесс
Являясь ведущим производителем светодиодных дисплеев в Китае, Enbon предлагает две серии продуктов для прямого подключения (DIP) и поверхностного монтажа SMD, которые полностью соответствуют требованиям различного расстояния между точками, визуальному расстоянию, яркости и экологическим требованиям для приложений.Создана полная система разработки, производства и управления качеством продукции. Она имеет 8 полностью автоматических импортных производственных линий SMT, 4 полностью автоматических печатных машины и 2 полностью автоматические линии сушки для наружной продукции, которые могут полностью удовлетворить потребности различных заказов и спецификации. Продукты прошли сертификацию CCC, FCC, CE, IAF, ROHS и других международных стандартов, сертификацию квалификации продукта и предприятия, отчет об испытаниях продукта и патентные сертификаты.
Проверка чипа светодиодного дисплея
Имеются ли механические повреждения и язвы на поверхности материала (размер стружки Локхилла и размер электрода соответствуют технологическим требованиям, рисунок электрода завершен).
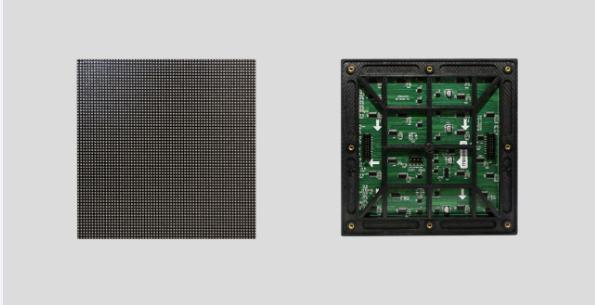
Светодиодный дисплей расширяется
Поскольку чип электронного светодиодного дисплея по-прежнему расположен близко после того, как срез небольшой (около 0,1 мм), это не способствует работе постобработки.Мы использовали развертку, чтобы расширить пленку приклеенного чипа, так что расстояние между светодиодными чипами увеличилось примерно до 0,6 мм.Также можно использовать ручное расширение, но это может привести к потере стружки и другим нежелательным проблемам.
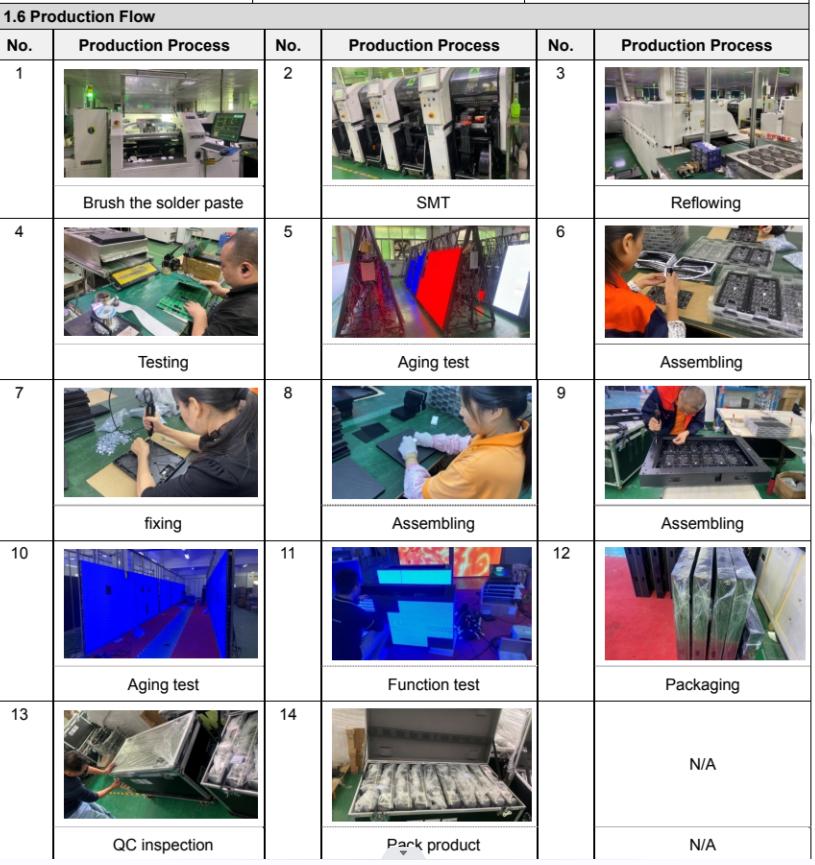
Светодиодное дозирование
Серебряный клей или изолирующий клей помещается в соответствующее положение кронштейна светодиодного дисплея.(Для проводящей подложки GaAs, SiC, красного света, желтого света, желто-зеленого чипа с задним электродом используется серебряный клей. Для чипов синего света и зеленого светодиода с сапфировой изолирующей подложкой для фиксации чипов используется изолирующий клей. Трудность Процесс заключается в контроле количества клея, высоты коллоида, положения клея. Подробные требования к процессу. Поскольку серебряный клей и изоляционный клей предъявляют строгие требования к хранению и использованию, времени пробуждения, смешивания и использования. Серебряный клей — это вопросы, на которые следует обратить внимание в процессе.
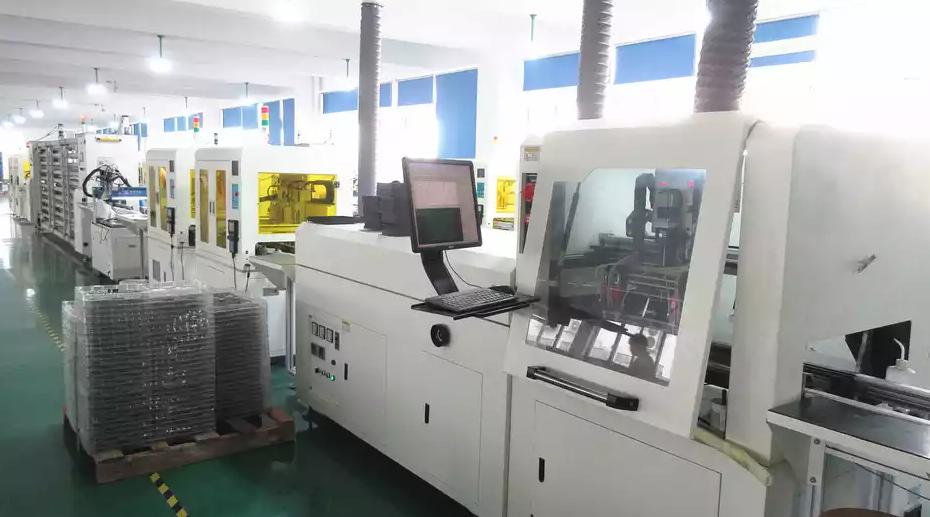
Светодиодное ручное прокалывание
Поместите расширенный светодиодный чип (с клеем или без него) на приспособление прокалывающего стола, поместите светодиодный кронштейн под приспособление и проколите светодиодный чип один за другим в соответствующее положение под микроскопом с помощью иглы.По сравнению с автоматическим монтажом у ручного монтажа чипов есть одно преимущество: в любой момент можно легко поменять разные чипы.Подходит для продуктов, требующих установки нескольких чипов.
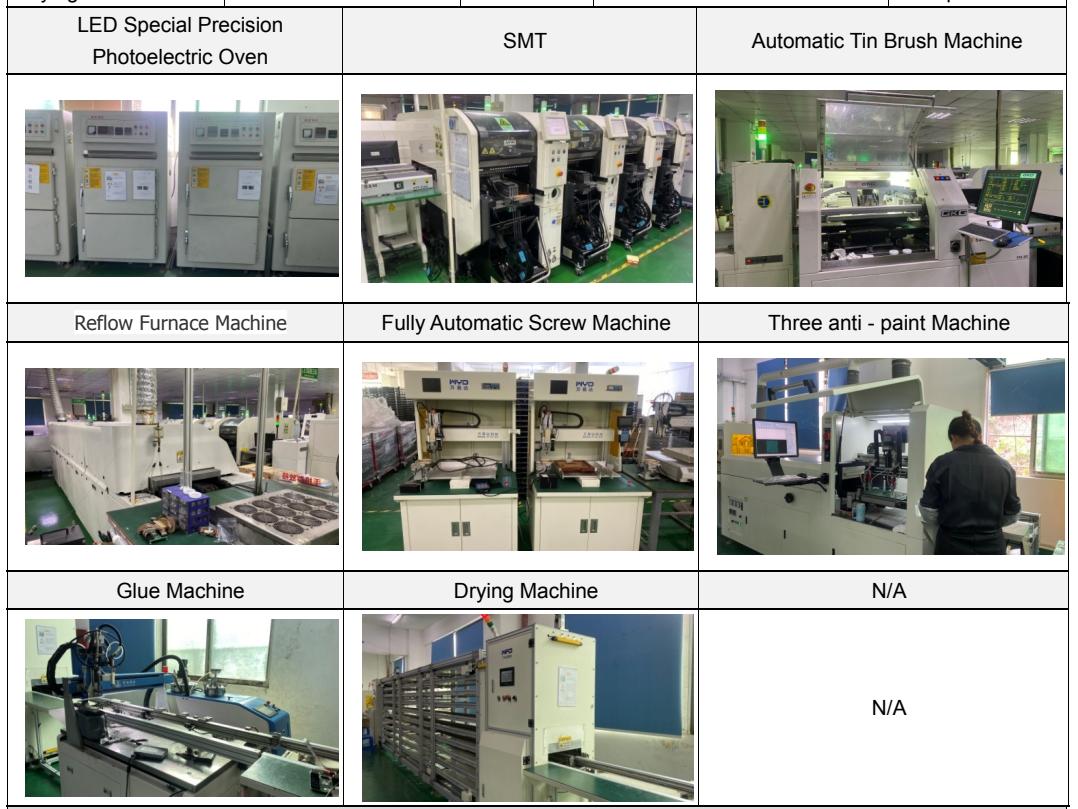
Автоматический монтаж светодиодного экрана
Автоматический монтаж на самом деле представляет собой комбинацию клея (дозирования) и установки чипа в два этапа: сначала нанесите серебряный клей на кронштейн светодиода (изоляционный клей), а затем используйте вакуумную насадку, чтобы всасывать движущееся положение светодиодного чипа, а затем помещайте его на соответствующее положение опоры.В процессе автоматической установки стойки мы должны ознакомиться с программированием работы оборудования, а также отрегулировать клей и точность установки оборудования.При выборе сопла, насколько это возможно, выбирайте бакелитовое сопло, чтобы предотвратить повреждение поверхности светодиодного чипа, особенно синего и зеленого чипа, мы должны использовать бакелит.Потому что насадка царапает текущий диффузионный слой на поверхности чипа.
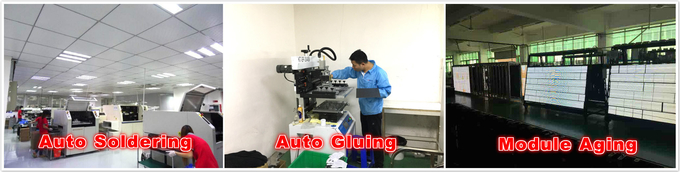
Светодиодное спекание
Целью спекания является затвердевание серебряного клея, а спекание требует контроля температуры, чтобы предотвратить плохое качество партии.Температура спекания серебряного клея обычно поддерживается на уровне 150 ℃, а время спекания составляет 2 часа.В зависимости от реальной ситуации можно отрегулировать температуру до 170 ℃, 1 час.Изоляционный клей обычно 150 ℃, 1 час.Печь для спекания серебряного клея необходимо открывать каждые 2 часа (или 1 час) в соответствии с требованиями процесса для замены спеченных изделий, а не открывать по желанию посередине.Во избежание загрязнения печь для спекания не должна использоваться для других целей.
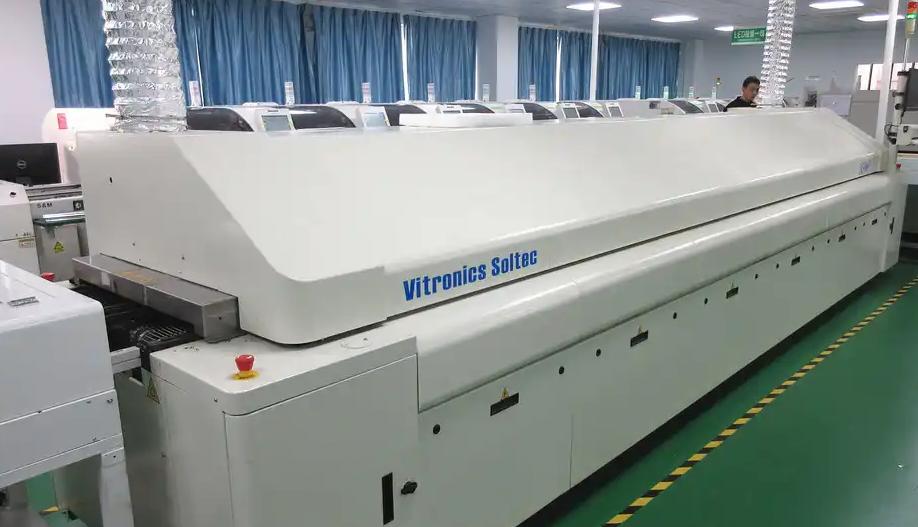
Светодиодная сварка под давлением
Целью сварки давлением является подведение электрода к светодиодному чипу и завершение соединения внутреннего и внешнего выводов изделия.Процесс сварки давлением светодиодного дисплея включает сварку шариками из золотой проволоки и сварку давлением алюминиевой проволоки двух видов.Сначала нажмите на первую точку электрода светодиодного чипа, затем протяните алюминиевый провод к соответствующему кронштейну, нажмите на вторую точку, а затем оттяните алюминиевый провод.Процесс сварки шариком из золотой проволоки заключается в обжиге шарика перед нажатием на первую точку, а остальная часть процесса аналогична.Сварка под давлением является ключевым звеном в технологии упаковки больших светодиодных экранов.Основным процессом, который необходимо контролировать, является сварка давлением золотой проволоки (алюминиевой проволоки), форма дуги, форма паяного соединения, натяжение.
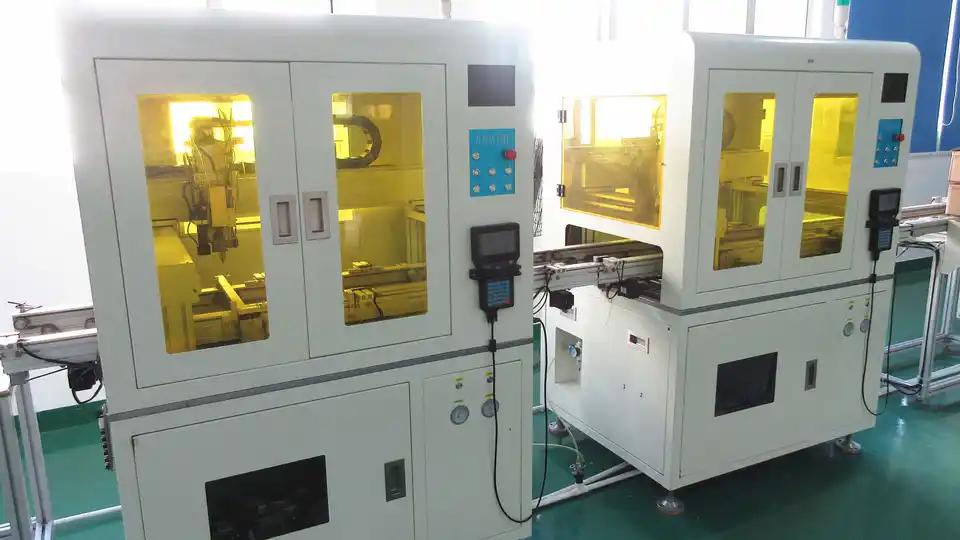
Светодиодный герметик
В упаковке светодиодных электронных экранов используются методы клея, заливки и формования.Проблемы управления процессами включают управление пузырьками, количеством материала и «черными точками».При проектировании основное внимание уделяется выбору подходящей комбинации эпоксидной смолы и подложки.Светодиодная выдача имеет варианты TOP-LED и Side-LED.Ручное дозирование требует точного контроля количества эпоксидной смолы.Нанесение белого светодиода может иметь различия в цвете из-за осадка люминофора.Клей для светодиодов и инкапсуляция ламп-светодиодов являются распространенными методами.При заливке в полость формы впрыскивается жидкая эпоксидная смола, которая затвердевает и формирует светодиод.Формование светодиодов включает в себя заполнение форм твердой эпоксидной смолой, которая затекает в канавки светодиодов и затвердевает.
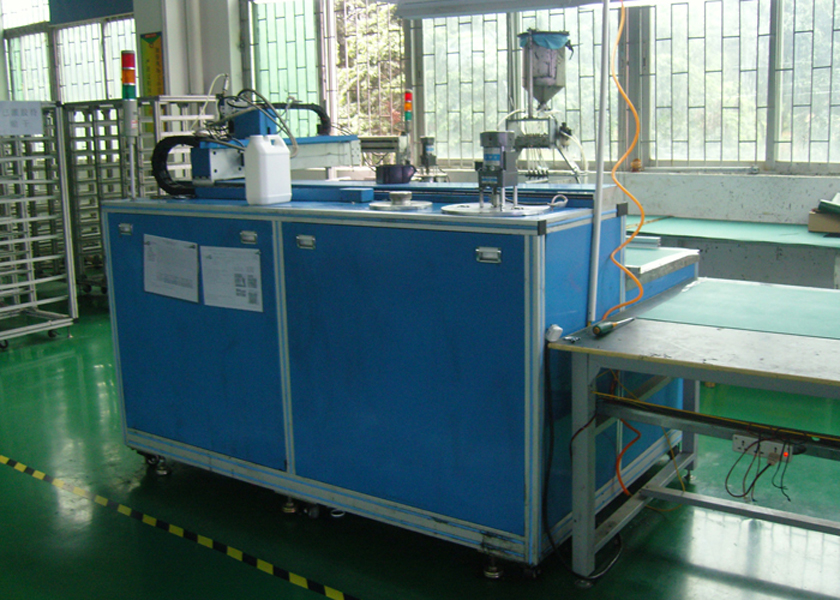
Светодиодное отверждение и пост-отверждение
Отверждение относится к отверждению герметизирующей эпоксидной смолы.Обычно время отверждения эпоксидной смолы составляет 135 ℃, 1 час.Формованная упаковка обычно находится при температуре 150 ℃ в течение 4 минут.Пост-отверждение заключается в том, чтобы позволить эпоксидной смоле достаточно затвердеть, пока светодиод подвергается термическому старению.Постотверждение очень важно для улучшения прочности соединения эпоксидной смолы и печатной платы.Общее состояние составляет 120 ℃ в течение 4 часов.
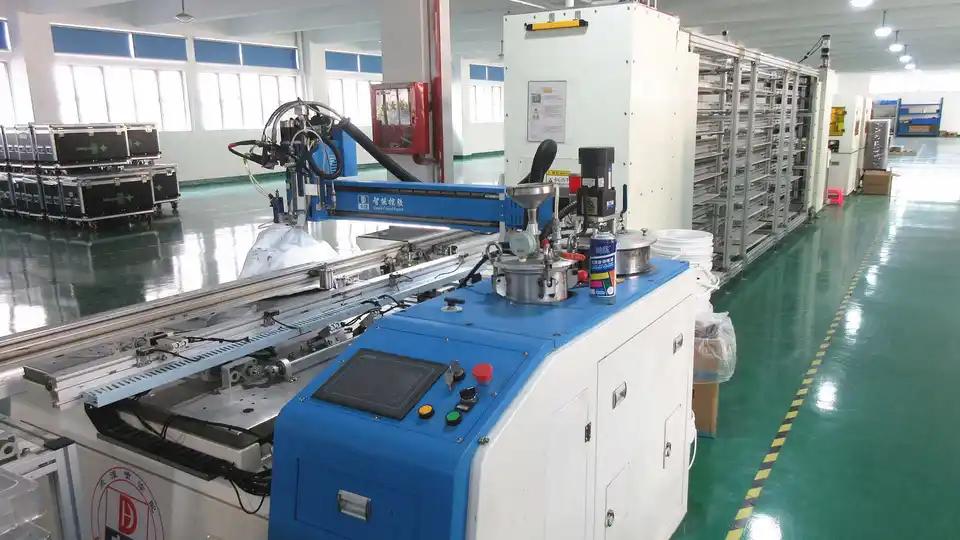
Светодиодная резка и нарезка ребер
Поскольку светодиодный экран при производстве соединяется вместе (а не один), в упаковке светодиодной лампы используется обрезка ребра, чтобы отрезать ребро светодиодного кронштейна.SMD-LED находится на печатной плате, и для завершения работы по разделению его необходимо разрезать на части.
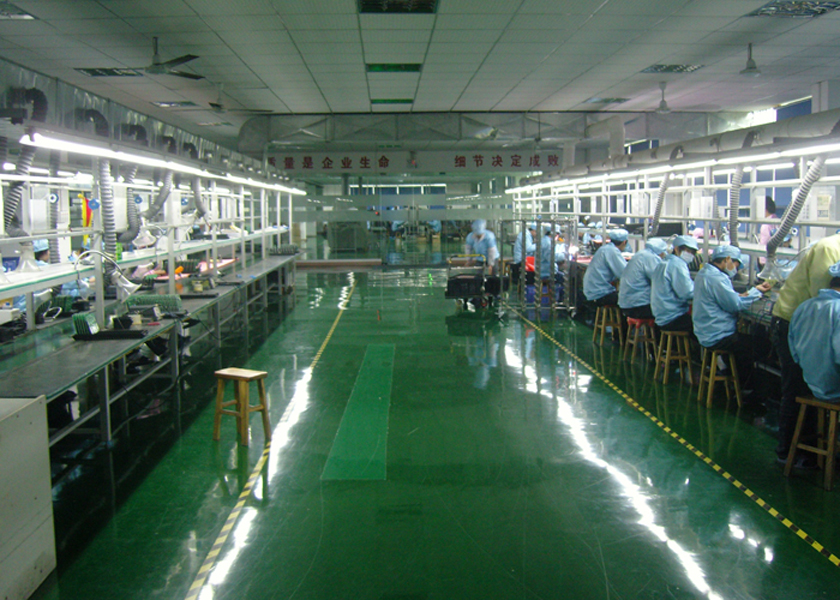
Тест светодиодов
Проверьте фотоэлектрические параметры светодиодов, проверьте форму и размер и отделите светодиодные электронные дисплеи в соответствии с требованиями заказчика.
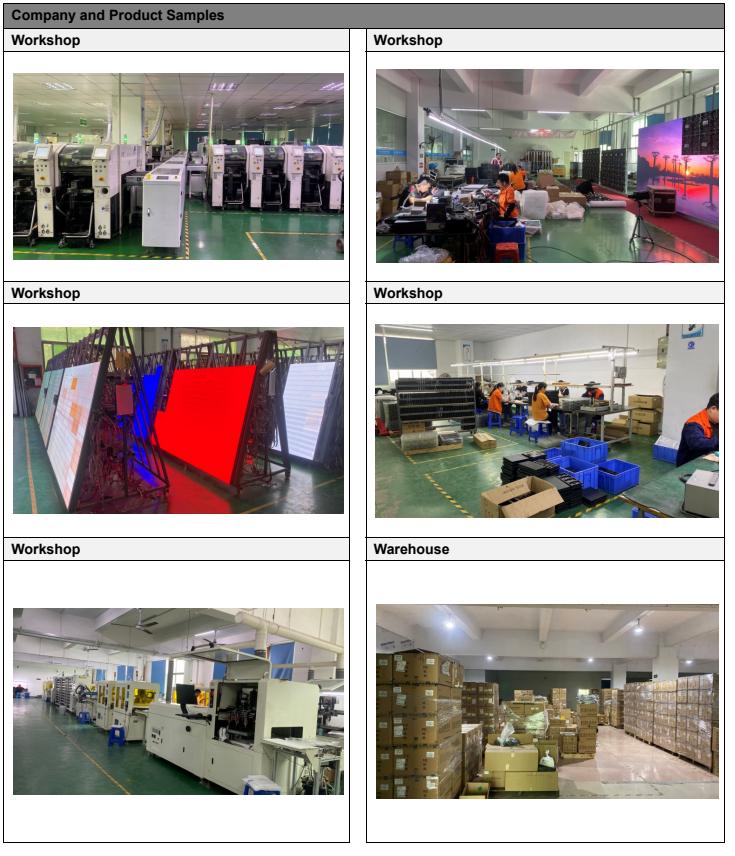
Процесс формирования шкафа
Коробка представляет собой соединение различных модулей, плоскостность коробки и зазор между модулями напрямую связаны с общим эффектом сборки коробки.В настоящее время широко используются коробки для обработки алюминиевых пластин и коробки из литого под давлением алюминия, плоскостность которых может достигать 10 проводов.Зазор сшивания между модулями оценивается по расстоянию между ближайшими пикселями двух модулей.Если два пикселя находятся слишком близко, загорится яркая линия;если два пикселя находятся слишком далеко, получится темная линия.Перед сборкой необходимо измерить и рассчитать место соединения формы, а затем заранее выбрать относительную толщину металлического листа в качестве приспособления для вставки при сборке.
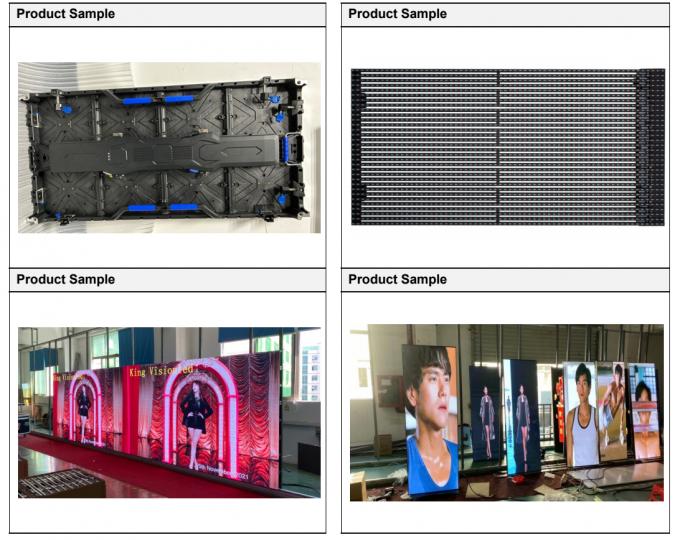
Водонепроницаемый процесс для аренды на открытом воздухе, твердые монтажные изделия
Процесс производства водонепроницаемой конструкции светодиодного дисплея.Его характеристикой являются следующие этапы:
● Коробка из алюминиевого сплава, отлитая под давлением;
● Гофрированная водонепроницаемая силиконовая прокладка устанавливается в гофрированную канавку в верхней части коробки из алюминиевого сплава;
● Печатная плата установлена и закреплена на гофрированной водонепроницаемой силиконовой подушке внутри коробки из алюминиевого сплава;
● Герметик впрыскивается в зазор печатной платы, зазор между краем печатной платы и краем корпуса из алюминиевого сплава, образуя водонепроницаемый слой.
● Закрепите маску на печатной плате.
Метод распыления светодиодного дисплея
● Конструкция формовочной коробки из металлического материала;
● Очистите конструкцию коробки и удалите с поверхности пыль;
● Нанесите слой алюминиевого порошка на внешнюю поверхность коробки;
● Установите заземляющее паяное соединение на слой алюминиевого порошка коробки и установите защитный слой на заземляющее паяное соединение;
● Пескоструйная обработка внутренней поверхности коробки и слоя алюминиевой пудры производится;
● Через некоторое время травление фосфатированием;
● Опрыскайте поверхность коробки после травления фосфатированием;
● Поверхность распыляемой коробки покрыта смолой.
Процесс проверки готовой продукции
● - После завершения упаковки готовой продукции в производственном отделе руководитель группы упаковки должен организовать отправку партий в зону ожидания для выборочного контроля в соответствии с различными заказами, разными моделями и партиями.Если количество заказа превышает 500 комплектов, каждые 500 комплектов будут считаться партией;Если количество заказа составляет менее 500 комплектов, все количество будет рассматриваться как одна партия для отправки контроля качества на выборочную проверку.
● Контроль качества готовой продукции должен соответствовать GB/T2828.1-2012 в соответствии с рабочими инструкциями и соответствующими стандартами. Уровень II после обычного выборочного контроля, в соответствии с AQL: серьезный дефект = 0, крупный дефект = 0,25, незначительный дефект = 1,0, протестировать и определить партию. готовой продукции и извлекайте 2 шт готовой продукции для каждого заказа для проверки на демонтаж: внешний вид и сочетание рабочего процесса, основные материалы должны соответствовать требованиям, а результаты выборочного контроля должны быть записаны в отчете о проверке готовой продукции.
● QA маркирует партии продуктов, которые были протестированы и проверены, для отслеживания и контроля состояния качества партий продуктов;
● Служба контроля качества должна проштамповать штамп «QA PASS» на боковой маркировке внешней коробки партии продукта после того, как она будет признана аттестованной, и уведомить производителя о необходимости передать продукт в зону аттестованного продукта или заняться складированием.
● Служба контроля качества обнаруживает несоответствующую продукцию при выборочной проверке, сообщает руководителю по обеспечению качества для подтверждения, маркирует и выпускает несоответствующую партию.Отчет о корректирующих и предупреждающих действиях > Или < Лист обработки исключений по качеству > Немедленно уведомите руководителя группы упаковки или руководителя производства производственного отдела, чтобы он подписал машину и переместил продукцию партии в несоответствующую зону.
● Если после отбора проб для обеспечения качества выявляются проблемы с внешним видом/упаковкой, производственный отдел должен проанализировать причину и принять корректирующие и профилактические меры.
● Если несоответствующий продукт является функциональной проблемой после подтверждения выборки для обеспечения качества, руководитель отдела обеспечения качества/техник технического отдела проанализирует причину несоответствующего продукта и заполнит результат анализа в <Отчете о корректирующих и предупреждающих действиях> Или < Лист обработки исключений по качеству > В столбце причины проблемы, если она вызвана проблемой человека/процесса/материала, технический отдел должен принять корректирующие и профилактические меры.
● При принятии корректирующих мер соответствующие отделы должны уточнить конкретные методы доработок и временных мер по улучшению, а руководитель отдела обеспечения качества должен подтвердить методы доработок в соответствии с мерами по улучшению.
● Производственный отдел должен переработать все неквалифицированные партии, отклоненные службой контроля качества, в соответствии с инструкциями по доработке, и снова отправить их в отдел контроля качества для выборочной проверки после того, как доработка будет квалифицирована, и они могут храниться и отправляться до тех пор, пока отдел контроля качества не будет квалифицирован для выборочного контроля.
● В процессе выборочного контроля, если основные дефекты продукта возникают два раза подряд в течение месяца и проблема та же самая, руководитель отдела обеспечения качества должен созывать технический отдел, производственный отдел и другой соответствующий персонал для проведения специальных проверок. рассмотреть и разработать контрмеры по улучшению.Служба контроля качества должна отслеживать результаты обработки и сообщать о результатах отслеживания генеральному менеджеру.
● Запись о качестве: отдел контроля качества должен суммировать результаты проверки готовой продукции каждый день, рассчитывать долю квалифицированных партий и долю дефектных образцов за день, а также составлять еженедельный отчет, чтобы знать состояние качества готовой продукции на этой неделе и отслеживать и фиксировать выполнение корректирующих и предупреждающих мер.ОК должен подвести итоги месячной проверки и подготовить ежемесячный сводный отчет о качестве с целью проверки достижения целей в области качества и в качестве основы для улучшения качества.